Revolution im Schaltanlagenbau
Vom Konfigurieren bis zu den Produktionsunterlagen:
Alles ohne Engineering!

Manfred Bickel, Leiter Elektroplanung
Wünschen Sie mehr Informationen? Wir freuen uns auf Ihre Kontaktaufnahme!
Telefon: +423 377 13 33 | E-Mail
In der sich ständig weiterentwickelnden Welt des Maschinen- und Anlagenbaus hat die rasch zunehmende Produktvielfalt eine neue Ära eingeläutet. Diese Entwicklung bringt erhebliche Herausforderungen mit sich, insbesondere für den Schaltanlagenbau. Denn der herkömmliche Prozess der Auftragsabwicklung entspricht mit seinen Methoden nicht mehr den Anforderungen, da die manuelle Erstellung von Unterlagen mithilfe traditioneller Werkzeuge zeitaufwendig und fehleranfällig geworden ist.
ECAD-Hersteller wie Zuken oder EPLAN bieten zwar mittlerweile grundlegende Möglichkeiten, Varianten und Optionen im Elektroschema abzubilden, doch dies reicht im Maschinenbau allein noch nicht aus, um eine nahtlose Ableitung von Fertigungsdokumenten zu gewährleisten.
Um diese Lücke zu schliessen, hat Pantec Methoden zur transparenten Darstellung von Optionen und Varianten entwickelt und gleichzeitig die Automatisierung der Datenverarbeitungsprozesse vorangetrieben.
Mit dem Ziel, die Abwicklung von Kundenprojekten vollständig in die Hand von Vertrieb und AVOR zu geben und damit das Engineering vom Tagesgeschäft zu befreien.
Rückblick: Die hohe Komplexität eines neuen Maschinensystems erfordert eine Neuausrichtung in der Elektroplanung
Es brauchte die Einführung einer neuen Maschinengeneration bei einem Kunden in der Druckindustrie, welche uns schonungslos vor Augen führte, dass die Prozesse in der Auftragsabwicklung für den Schaltanlagenbau den Anforderungen nicht mehr gerecht wurden. Zuvor standen wir bereits vor verschiedenen Herausforderungen im Zusammenhang mit Maschinenoptionen, doch in diesem Fall versagten selbst diese Prozesse.
Die hochperformanten Heissfolienprägeanlagen waren in verschiedenen Bahnbreiten, Folienbahnoptionen und Produktvarianten mit insgesamt 20 Optionen und 120 Varianten von erheblicher Komplexität und in der Auftragsabwicklung nur noch mit enormem personellen Aufwand - zu einem grossen Teil aus dem Engineering - zu stemmen.

Das Hochleistungsheissprägesystem CHEETAH: 20 Optionen und 120 Varianten brachten den Auftragsabwicklungsprozess für die Schaltanlage mit klassischer Elektroplanung an seine Grenzen.
Die Komplexität der Produktvarianten stellte den herkömmlichen Auftragsabwicklungsprozess vor erhebliche Herausforderungen. Die Erfassung von Kundenaufträgen erforderte fundiertes Maschinen-Know-how, das Engineering war stark involviert, und der Prozess zur Erstellung von Dokumenten war kompliziert und fehleranfällig. Zusätzlich zu diesen typischen Anforderungen im Maschinenbau kam die Tatsache hinzu, dass sich die Bestellspezifikationen oft kurzfristig in der Produktion änderten – eine Situation, die nur durch grossen Aufwand und unter Einbeziehung des Engineerings bewältigt werden konnte.
Konventionelle Informationsinseln und „Copy Paste Schema“ als Grundproblem
Die elektroplanerischen Aktivitäten waren zu diesem Zeitpunkt auf verschiedene Systeme verteilt: Die Schema-Darstellung erfolgte im ECAD (weitgehend grafisch und oberflächlich), die Komponentenplatzierung in einer mechanischen CAD und die Artikelverwaltung im ERP-System. Eine Änderung in einem System erforderte normalerweise eine entsprechende Änderung in den anderen Systemen.
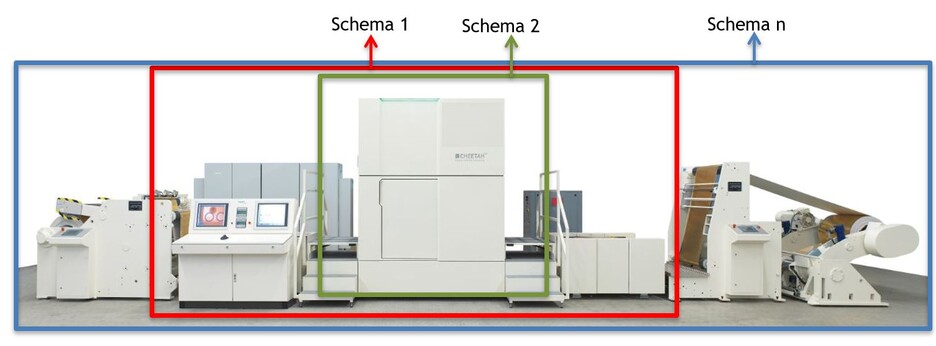
Klassische Copy-Paste Schema Struktur: für jeden Kundenauftrag wird – basierend auf den Elektroschemas vergangener Aufträge – mit hohem Engineeringaufwand ein weiteres Schemaderivat erzeugt. Auf dieser Basis müssen dann im Folgenden die Fertigungsdokumente für jeden Auftrag – oft manuell und von 0 auf – neu erstellt werden.
Das Kernproblem jedoch lag in der Art der Schema-Erstellung. Jede Kundenanlage erforderte ein neues Schema, das zwar auf einer Struktur von Varianten und Optionen basierte, jedoch manuell an die neuen Gegebenheiten angepasst werden musste. Anschliessend mussten sämtliche Fertigungsdokumente wiederum manuell erarbeitet werden. Ein fehlerhafter, arbeitsintensiver und damit teurer Prozess, der zudem wertvolle Engineeringressourcen gebunden hat.
Weiterentwicklungen im ECAD Bereich und Schnittstellen ermöglichen konfigurierbares Schema und zentrale Verwaltung der Daten
Durch eine grundlegende Weiterentwicklung der ECAD Systeme (von grafischen Symbolen hin zu objektorientierten Komponenten) sowie der Bereitstellung neuer Funktionen zur Abbildung von Optionen und Varianten wurde das Fundament für eine konzeptionelle Neuausrichtung der Elektroplanung gelegt. Nun war es möglich, in einem Masterschema alle möglichen Produktausprägungen abzubilden und über die Optionen-/Variantenauswahl ein Auftragsschema zu kommissionieren. Zudem war es möglich, durch das objektorientierte Design die bis dato in der grafischen Darstellung verborgene Intelligenz in der (objektorientierten) Komponente darzustellen - was die Grundlage für die automatisierbare Verarbeitung der Schemadaten darstellt.
Beispiel: Verbindung von Anschluss X1 eines Relais mit Anschluss X2 einer Sicherung
konventionelles ECAD: grafische Darstellung der Verbindung dieser beiden Komponenten, allerdings ist die Information nur für den verfügbar, der die Darstellung sieht.
Objektorientiertes ECAD: dem Symbol der Komponente selbst sind Metadaten angehängt, die die Information der Verbindung datentechnisch verfügbar machen. Diese Information lässt sich für eine weitere Verwertung (z.B. Drahtzugliste, Litzenset, Routing im Schaltschrank) nutzen.
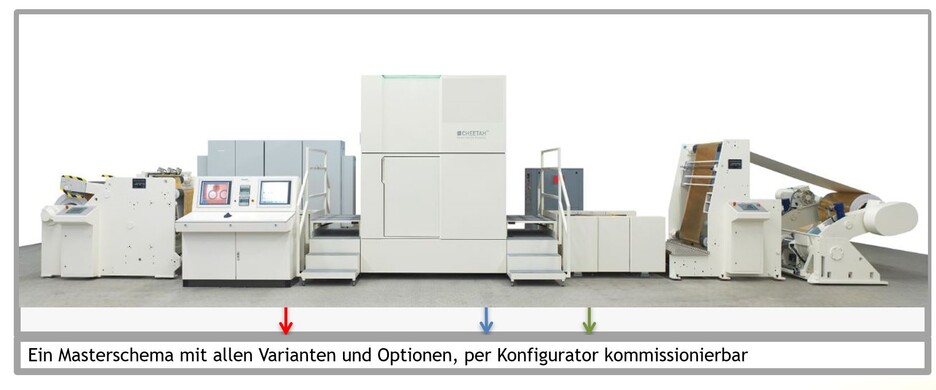
Mit Erweiterungen in den Bereichen Modularität, Variantenhandling und Topologieplanung ermöglichen die Hersteller von ECAD Lösungen neue Lösungsansätze für die wachsende Varianten- und Optionenvielfalt. So lassen sich aus einem allgemein gültigen Masterschema per Konfigurator kommisionierte Auftragsschemas ableiten.
Ein weiteres zu lösendes Problem war die Datenverteilung auf verschiedene Systeme. Neue Schnittstellentechnologien und Datenstandards wie ECl@ss ermöglichten die Konzentration der Daten aus verschiedenen Systemen in einer zentralen Datenbank. Dadurch entfiel die zeitaufwändige Anpassung von Änderungen in verschiedenen Systemen.
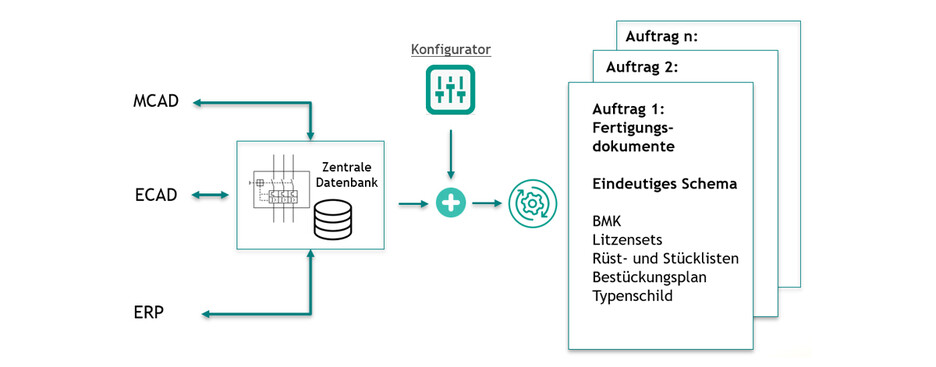
Ein Masterschema mit Optionen und Varianten in Kombination mit einer zentralen Datenbank ermöglicht das einfache Ausleiten von spezifischen Auftragsdaten wie Kommissionierschema und Fertigungsunterlagen per Konfigurator.
Die Perfektionierung des Prozesses: Arbeitsmethoden und viele kleine Helferlein
Das optionierbare Schema und die zentrale Zusammenfassung standardisierter Daten legten das Fundament für einen umfassenden digitalen Zwilling, der alle Informationen von Komponenten über Verbindungen bis hin zu Kabel- und Betriebsmittelkennzeichnungen enthielt.
Jedoch fehlten noch Methoden und Werkzeuge, um den Prozess erfolgreich in einer Organisation umzusetzen und die Effizienz der Arbeit zu steigern. Mit der finalen Bereitstellung von Methoden und Automatisierungs-Scripten wurde auch diese Lücke geschlossen:
Die wichtigsten Bausteine sind:
- Data Editor: Die Abbildung von Optionen und Varianten in ECAD Tools ist relativ unübersichtlich. Ein strukturierter Daten Editor schafft Transparenz und ist Grundlage für einen automatisierten Transfer ins ECAD Tool
- ECAD Import: bringt die strukturierten Daten vom Data Editor in das Source Project vom ECAD. Das beinhaltet neben der Teile Liste auch die Optionen und Varianten
- Publish: Werkzeug für die Erstellung spezifischer Berichte, sortiert nach Wunsch (Inhaltsverzeichnis, Elektroschema, BOM, ....)
- Data Collector: Tool zur spezifischen Aufbereitung der Datenbankinformationen für Drittsysteme (z.B. für die Kabelfertigung, Baugruppenherstellung, Schaltschrankaufbau, Routing, etc.)
- Konfigurator: Einfach zu handhabendes Werkzeug zur Abbildung der spezifischen Kundenbestellung ohne jegliches Know How der möglichen und unzulässigen Kombinationen.
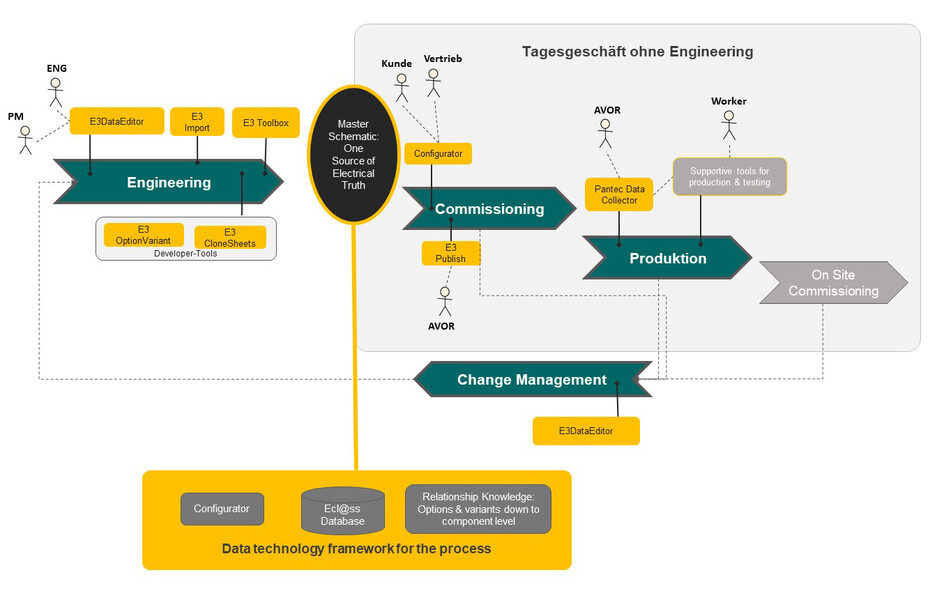
Die kundenspezifische Standardmaschine mit Blick auf den Schaltanlagenbereich. Das Tagesgeschäft - sprich die Abwicklung der Kundenaufträge - läuft unabhängig vom Engineering über den Vertrieb und die AVOR
Integrierter Auftragsabwicklungsprozess für Schaltanlagen: automatisches Erstellen des Panellayouts inklusive!
Die hohe Varianten- und Optionenvielfalt bei Maschinen und Anlagen erfordert den Einsatz neuer Methoden und Technologien, um den Schaltanlagenbau auch zukünftig effizient und flexibel realisieren zu können.
Der Auftragsabwicklungsprozess kann so unabhängig vom Vertrieb angestossen und von der Arbeitsvorbereitung (AVOR) abgewickelt werden – alles ohne Engineering
➡️ Der Vertrieb erstellt mit Hilfe eines Produktkonfigurators die Zusammenstellung der Maschine
➡️ Diese Daten werden von AVOR mithilfe des Tools „ECAD import“ ins Zuken E3 übernommen und ein Masterschema für die spezifische Konfiguration erstellt
➡️ Mit dem Tool „E3 Publish“ werden die Fertigungsdokumente (Schema, BOM, Prüflisten etc.) auf Knopfdruck generiert
➡️ Als Highlight – wie im Video gezeigt - können die Daten aus E3 in Solid Edge® von Siemens importiert werden, wo dann auf Basis der in den Artikeldaten hinterlegten Positionsbezeichnungen das Panellayout automatisch erstellt wird
Die praktische Umsetzung am Beispiel des Flachprägesystems RHINO
Das Flachprägesystem RHINO X stellt unser neuestes Projekt dar, bei dem wir als Partner im Schaltanlagenbau sowohl für die Elektroplanung als auch die Auftragsabwicklung der Schaltanlagen verantwortlich sind. Auch hier bewegt sich die Komplexität der Maschine wieder in einem Bereich, der ohne moderne Entwicklungstools kaum zu bewältigen wäre.
RHINO® X bringt hochwertige Veredelung und kosteneffizienten Markenschutz in die flexible Verpackungsindustrie. Als Offline-Konfiguration mit einer Bahngeschwindigkeit von bis zu 200 m/min ist RHINO® X eine wertvolle und produktive Ergänzung der Möglichkeiten jeder flexiblen Druckerei.
Die Abwicklung von Kundenbestellungen, selbst bei X Optionen und Y Varianten, erfolgt mithilfe des Pantec Prozesses äusserst effizient und flexibel.
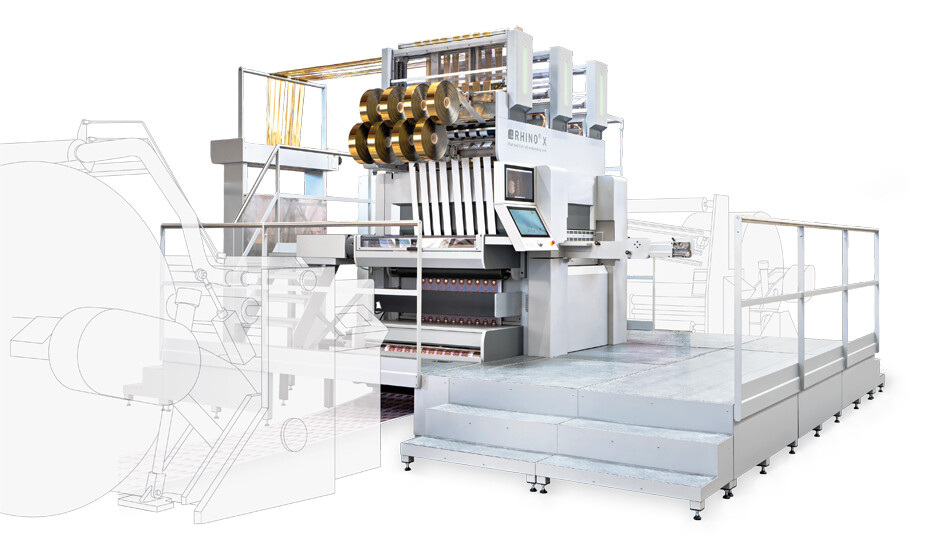
Offline-Prägesystem RHINO X: Selbst bei 24 Optionen die in 83 verschiedenen Varianten konfiguriert werden können ist der Auftragsabwicklungsprozess von Vertrieb und AVOR steuerbar, ohne dabei auf die Unterstützung des Engineering-Teams angewiesen zu sein.
.
RHINO X: Auftragsabwicklungsprozess der Schaltanlage
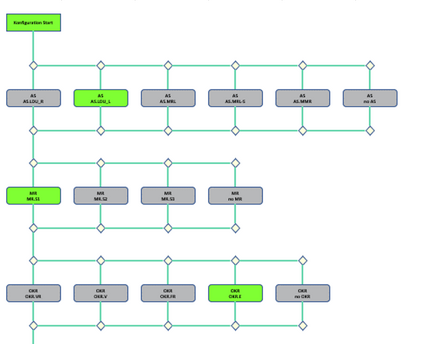
1. Auftragskonfiguration festlegen
Der Vertrieb des Maschinenbauers definiert gemeinsam mit dem Kunden am Konfigurator den Auftrag. Durch Plausibilitätsprüfungen und andere Checks ist eine gültige Konfiguration sichergestellt.
Das Konfigurationsfile wird in Folge der Pantec Arbeitsvorbereitung zur Aufbereitung der Produktionsunterlagen bereitgestellt.
Das Konfigurationsfile kann - bei entsprechender Implementierung beim Maschinenbauer - auch für die mechanische Herstellung der Maschine genutzt werden.
2. Auftragsschema kommissionieren
Der AVOR Mitarbeiter lädt das ECAD-Masterfile in einem Viewer Programm und importiert das Konfigurationsfile zur Anpassung auf den Kundenauftrag.
Damit liegt das kommissionierte Auftragsschema vor.

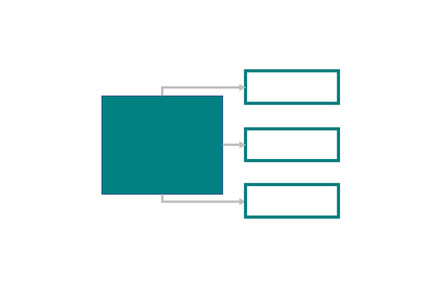
3. Fertigungsunterlagen erstellen
Mit Hilfe des Pantec Publishers werden Fertigungsunterlagen wie das kommissionierte Schema, BOM, Prüflisten etc. auf Knopfdruck generiert.
Zudem wird für die Montage und Prüfung ein digitales Datenset erstellt, welches die Source für diverse Hilfetools in der Produktion darstellt.
4. Montage und Verdrahtung
Der Monteur bekommt die Auftragsdaten in digitaler Form auf einem Tablett bereitgestellt. Dabei unterstützen ihn Tools wie der Panel Designer (zeigt die Bestückung der Schaltanlage) und das Wiring Cockpit (angeleitete Verdrahtung der Komponenten) bei der effizienten Erledigung seiner Arbeit.
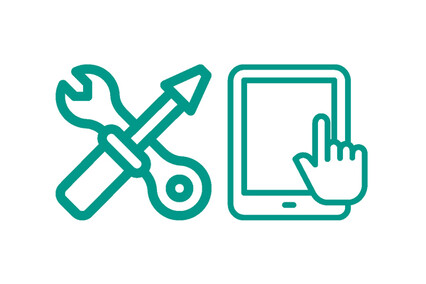
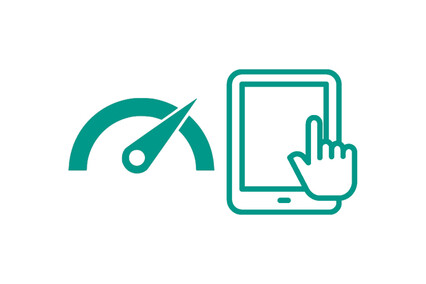
5. Prüffeld
Auch der Prüffeldmitarbeiter bekommt seine Unterlagen wie Prüfanleitungen, Prüfprotokolle und Checklisten digital bereitgestellt.
6. Auftragsänderungen
Im Falle von Änderungen während der Produktion werden diese im Konfigurator erfasst, die Aktualisierung der Fertigungsdaten erfolgt wieder in der AVOR wie unter Punkt 2. beschrieben.
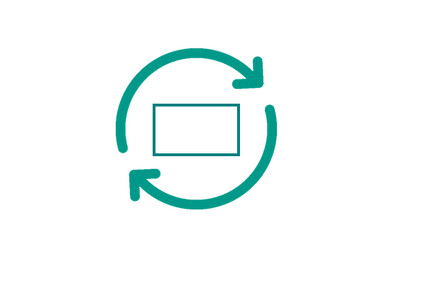
Die Benefits mit dem integrierten Schaltanlagenprozess von Pantec
Einsetzbar ab Losgrösse 1
Beim Thema Modularisierung herrscht oft der Glaube vor, dass sich das nur bei hohen Stückzahlen lohnt. Durch das vollständige Masterschema (mit korrekten Daten bis auf Komponentenebene) wird Modularisierung ab Losgrösse 1, damit also auch im Anlagenbau, effizient möglich!
Massive Entlastung des Engineerings
Durch die Bereitstellung der Schemadaten in Form einer "Master schematic one electrical source of truth" wird das Tagesgeschäft - sprich die für die Angebotsausarbeitung notwendige Konfiguration - selbständig vom Vertrieb durchgeführt. Auch die Ausleitung der Fertigungsdokumente läuft unabhängig in der Arbeitsvorbereitung.
Vereinfachte Logistik
Die integrierte Datenstruktur ermöglicht eine wirtschaftliche Planung bei unpräzisen und dynamischen Planungsdaten. So kann die Planung auf Basis von Standardkonfigurationen grundsätzlich geplant und bei Bedarf einfach auf konkrete Konfigurationen angepasst werden, ohne dass aufwändig die logistikrelevanten Dokumente wie BOM manuell angepasst werden müssen.
Schaltanlagenproduktion
Die unmittelbare Ausleitung der Fertigungsdokumente aus der Konfiguration stellt sicher, dass in der Produktion zu jedem Zeitpunkt vollständige und richtige Daten zur Verfügung stehen.
Einfache Maschinenupgrades
Durch die Bereitstellung von Änderungslisten können für bestehende Anlagen hardwaretechnische Nachrüstungen einfach durchgeführt werden.
Sie wollen auch einen Prozess zur Schaltanlagenfertigung, der Ihr Engineering massiv entlastet und Ihrem Vertrieb einen Kompetenzboost gibt?
Wir demonstrieren Ihnen gerne in einem halbstündigen Webmeeting den Prozess von der Konfiguration der Maschine/Schaltanlage bis zur digitalen Bereitstellung der kommissionierten Fertigungsdokumente. Als Draufgabe sehen Sie noch, wie die Monteure durch verschiedene Tools bei ihrer Arbeit unterstützt werden.
Interessiert?
Ich freue mich sehr, Ihnen entweder in einem Webmeeting oder bei einem persönlichen Gespräch vor Ort mehr über die erfolgreiche Einführung eines Steuerungssystems zu erzählen.
Schreiben Sie mir einfach eine E-Mail - ich melde mich bei Ihnen!
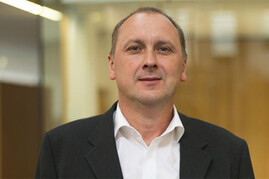
Manfred Bickel
Leiter Elektroplanung
T: +423 377 13 33
E-Mail