Modularisierung und Standardisierung
Das kundenspezifische Standardsystem: Ein Schlüssel zur Bewältigung zentraler Herausforderungen im Maschinen- und Anlagenbau

Stefan Safran, Leiter Business Unit Automation
Sie wollen mehr Infos? Ich freue mich auf Ihre Kontaktaufnahme!
Telefon: +423 377 13 33 | E-Mail
Als das Heißfolienprägesystem CHEETAH™ aufgrund hoher Nachfrage aus dem chinesischen Markt sprichwörtlich durch die Decke ging, stand der Hersteller vor der nahezu unlösbaren Aufgabe, die Aufträge fristgerecht und mit vertretbarem Ressourceneinsatz umzusetzen. Zu diesem Zeitpunkt war die Maschine als Spezialmaschine konzipiert, was bedeutete, dass sie für jeden Kundenauftrag individuell angepasst wurde – ein Prozess, der hohe Aufwände in Konstruktion und Montage verursachte.
Durch die Einführung eines Baukastensystems wurde aus der einstigen Spezialmaschine eine konfigurierbare Standardmaschine, die heute mithilfe eines Konfigurators definiert und direkt in die Produktion überführt werden kann. Dies führte zu einer erheblichen Entlastung der Konstruktion und reduzierte die Durchlaufzeiten der Systemkomponenten um mehr als die Hälfte. Das Ergebnis: eine verbesserte Lieferfähigkeit bei deutlich optimierter Kostenstruktur – ein entscheidender Baustein für die Marktführerschaft.
Die gute Nachricht: Mit der richtigen Methodik lassen sich sowohl ursprünglich starr konzipierte Serienmaschinen als auch Anlagen, deren Variabilität bisher nicht standardisierbar schien, in ein solches Baukastensystem überführen. Dieser Ansatz bietet eine vielversprechende Lösung für die drängenden Herausforderungen im Maschinen- und Anlagenbau.
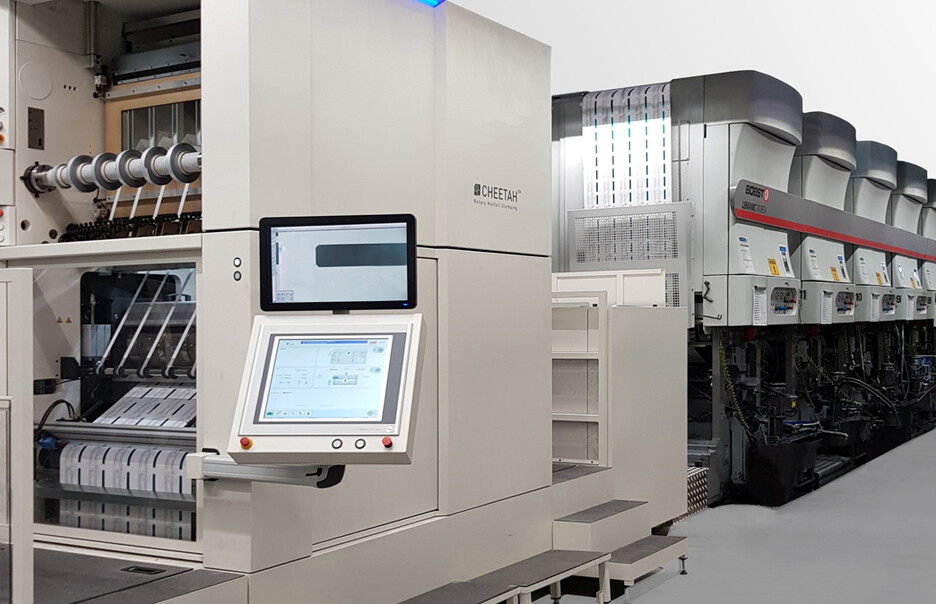
Das rotative Hochleistungs-Heissfolienprägesystem CHEETAH™ wurde vor der Umstellung auf ein Baukastensystem aufwändig als komplexe Sondermaschine hergestellt und ist heute als konfigurierbares System verfügbar. Die Maschinenbestellungen werden in 95 % der Fälle über einen Konfigurator abgebildet, für Spezialentwicklungen stehen offene Schnittstellen zur Verfügung.
Die zentralen Herausforderungen des Maschinenbaus
Der Maschinen- und Anlagenbau steht vor einer Vielzahl komplexer Herausforderungen, die Unternehmen in ihrem Wachstum und ihrer Innovationskraft bremsen können. Neben äußeren Faktoren wie dem zunehmenden Wettbewerb und steigenden Kundenerwartungen sind es oft auch interne Hürden, die es zu überwinden gilt. Diese betreffen nicht nur die Effizienz und Flexibilität der Produktion, sondern auch die Skalierbarkeit und die Abhängigkeit von Schlüsselkompetenzen. Die folgenden fünf Punkte beleuchten die zentralen Probleme, mit denen viele Unternehmen heute konfrontiert sind, und zeigen auf, wie sie langfristiges Wachstum und die Anpassungsfähigkeit behindern können.
1. Fehlende Skalierbarkeit
Viele Unternehmen können ihre Wachstumskurse nicht wirtschaftlich umsetzen, da die Grundlagen für Skalierbarkeit fehlen. Steigende Umsätze bedeuten zwangsläufig auch steigende Kosten und eine dauerhafte Überlastung der Mitarbeiter – eine Situation, die langfristiges Wachstum behindert.
2. Hohe Abhängigkeit von Mitarbeiter-Experten
Ein weiteres internes Problem ist die starke Abhängigkeit von Expertenwissen. Die meisten Maschinenbauunternehmen sind auf das Wissen und die Erfahrung einzelner Mitarbeiter angewiesen, was die Kontinuität und den Wissenstransfer erschwert und Risiken für die Innovationsfähigkeit birgt.
3. Abhängigkeit von Schlüsselkomponenten
Die Abhängigkeit von Lieferanten für Schlüsselkomponenten kann die Flexibilität und Reaktionsfähigkeit eines Unternehmens erheblich einschränken. Produktionsverzögerungen aufgrund von Lieferengpässen sind eine häufige Folge.
4. Steigende Komplexität bei Integrationen
Kundenprozesse werden immer komplexer, was neue Anforderungen an die Integration von Maschinen in bestehende Produktionsumgebungen stellt. Diese ständige Weiterentwicklung erhöht den Druck auf die Entwicklungsabteilungen und führt zu einer Überlastung der Ressourcen.
5. Wachsende Anforderungen an die Automatisierung
Unternehmen müssen ihren Automatisierungsgrad erhöhen, um ihre Effizienz zu steigern und wettbewerbsfähig zu bleiben. Dies erfordert nicht nur neue technologische Ansätze, sondern auch eine tiefere Integration von Systemen und Prozessen.
Der Kunde will ein perfekt passendes Maschinensystem
Auf der Kundenseite besteht die zentrale Herausforderung darin, ein Maschinensystem zu liefern, das perfekt auf die spezifischen Anforderungen zugeschnitten ist. Gleichzeitig müssen diese Maschinen nahtlos in die bestehende Produktionsinfrastruktur integriert und den Anforderungen der digitalen Fabrik gerecht werden. Das bedeutet, dass Maschinen nicht nur hochproduktiv, sondern auch flexibel und zukunftssicher sein müssen.
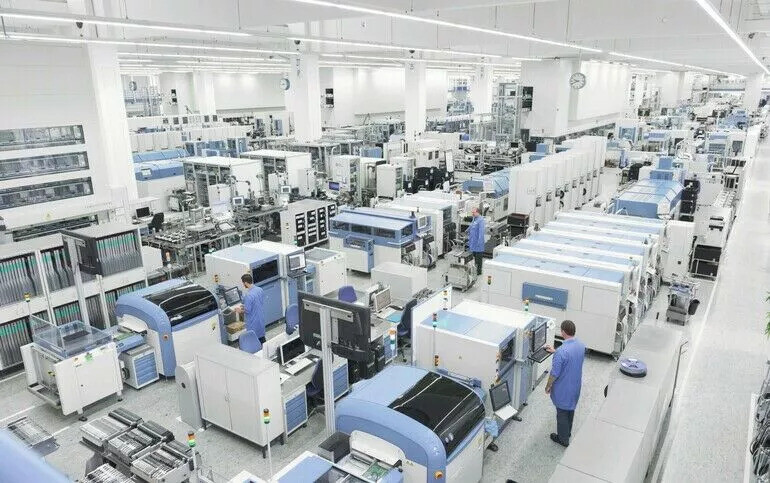
Die Herausforderung: Hochproduktive, kundenspezifische Maschinensysteme nahtlos in digitale Fabriken integrieren
Die heutige Herangehensweise – Ineffizient und teuer
Viele Maschinenbauunternehmen verarbeiten jede Kundenanfrage individuell über die Entwicklungsabteilung. Diese Praxis führt zu überlasteten Ressourcen, Verlusten von Aufträgen und Innovationsstaus. Ingenieure sind in der Auftragsabwicklung gebunden, was ihre Kapazität für Neuentwicklungen einschränkt. Hinzu kommt die zunehmende Komplexität der Anforderungen, die oft an den Kapazitäten der Entwicklungsabteilungen scheitern.
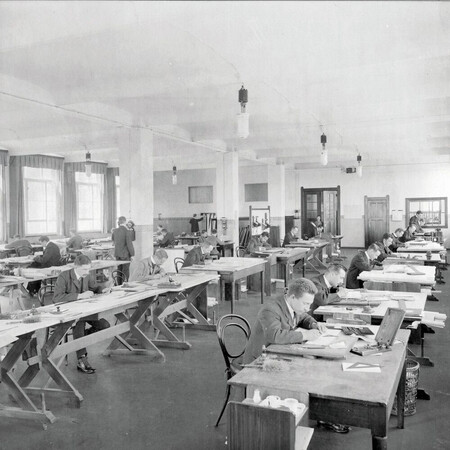
Die heutigen Werkzeuge im Maschinen- und Anlagenbau sind deutlich moderner als die im Bild dargestellten, doch das bedeutet nicht zwangsläufig, dass deren Potentiale genutzt und damit die Prozesse effizienter gestaltet sind
Die Abhängigkeit von Expertenwissen ist in dieser Situation besonders problematisch, da die Innovationsfähigkeit und Zukunftssicherheit des Unternehmens gefährdet ist. Oftmals ist die Entwicklungsabteilung auch in den After-Sales-Support eingebunden, was die Belastung weiter erhöht.
Das „kundenspezifische Standardsystem“ - Lösung zentraler Herausforderungen
Das kundenspezifische Standardsystem beschreibt ein Maschinenkonzept, das die Flexibilität einer maßgeschneiderten Lösung mit der Effizienz und Kostenvorteilen einer standardisierten Plattform kombiniert. Es basiert auf einem modularen System, das individuell an die spezifischen Anforderungen des Kunden angepasst werden kann, ohne die typischen Herausforderungen und Mehrkosten einer kundenspezifischen Weiterentwicklung. So entsteht eine perfekte Balance zwischen Anpassungsfähigkeit und bewährter Technik, die es Maschinen- und Anlagenbauern ermöglicht, schnell auf Kundenwünsche zu reagieren und gleichzeitig die Produktion zu optimieren.
Maschinentypen und ihre Modularisierungspotentiale
Der Aufwand für die Standardisierung darf nicht unterschätzt werden und muss immer im Zusammenhang mit den daraus resultierenden Vorteilen betrachtet werden. Entscheidend ist dabei der Maschinentyp, da die optimale Granularität der Standardisierung stark variiert und die notwendige Flexibilität nicht beeinträchtigt werden darf. Das richtige Gleichgewicht zu finden, ist der Schlüssel zu einem optimalen Kosten-Nutzen-Verhältnis.
Das begleitende Bild verdeutlicht, dass eine stufenlose Granularität von der Modulebene bis hin zur Maschinenebene möglich ist – je nachdem, in welchem Umfang der Maschinenbauer bereit ist, die Variantenvielfalt zugunsten einer höheren Standardisierbarkeit zu reduzieren.
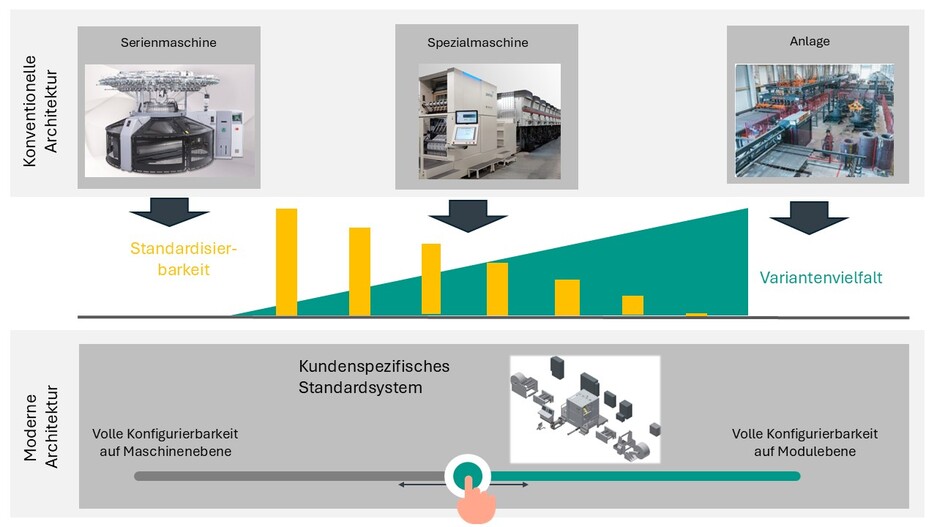
Die gute Balance zwischen Standardisierung und Flexibilität ist abhängig vom Maschinentyp und entscheidend für ein optimales Kosten-Nutzen-Verhältnis.
Im Maschinen- und Anlagenbau gibt es verschiedene Typen von Maschinen, die jeweils unterschiedliche Anforderungen an Standardisierung und Individualisierung stellen. Ob komplexe Anlagen, Spezialmaschinen oder Serienmaschinen – jede Kategorie bietet Potenzial für di Abbildung als kundenspezifisches Standardsystem. Durch modulare Bauweisen und gezielte Anpassungen lassen sich maßgeschneiderte Lösungen entwickeln, die Flexibilität und Effizienz vereinen. Im Folgenden werden die drei Maschinentypen detailliert beschrieben und die Möglichkeiten des kundenspezifischen Standardsystems in jedem Kontext aufgezeigt.
1. Anlage
Definition
Eine Anlage ist ein komplexes System, das aus mehreren Maschinen oder Komponenten besteht, die gemeinsam einen umfassenden Fertigungsprozess abdecken. Sie beinhaltet oft eine Kombination aus Spezialmaschinen, Serienmaschinen und anderen technischen Geräten, die in einer vernetzten Struktur zusammenarbeiten, um komplette Produktionslinien oder größere Fertigungsprozesse zu bewältigen.
Charakteristika
- Besteht aus mehreren Maschinen oder Modulen, die für einen kompletten Produktionsprozess zusammengestellt werden.
- Integriert sowohl Maschinen als auch Steuerungs- und Automatisierungssysteme.
- Oft maßgeschneidert und auf bestehenden, modifzierten Komponenten umgesetzt
Beispiele
- Eine vollautomatische Produktionslinie in der Automobilindustrie, die aus mehreren spezialisierten und serienmäßigen Maschinen besteht.
- Eine Lebensmittelverpackungsanlage, die Produkte sortiert, abfüllt, versiegelt und verpackt.
In komplexen Anlagen ist die Umsetzung eines kundenspezifischen Standardsystems besonders wertvoll. Einzelne Maschinen oder Module innerhalb der Anlage können standardisiert werden, während andere spezifische Anpassungen erfahren, um den gesamten Produktionsprozess optimal zu gestalten. Dies schafft ein flexibles, skalierbares System, das die Vorteile der Standardisierung in einem groß angelegten Fertigungskontext einbringt, ohne die erforderliche Individualisierung für den Gesamtprozess zu opfern.
2. Spezialmaschine
Definition
Eine Spezialmaschine, auch Sondermaschine genannt, ist eine individuell entwickelte Maschine, die für eine spezifische Aufgabe oder einen besonderen Fertigungsprozess konzipiert wurde. Sie wird oft speziell für die Bedürfnisse eines bestimmten Kunden oder einer spezifischen Anwendung angefertigt und erfüllt eine maßgeschneiderte Funktion.
Charakteristika
- Entwickelt für eine spezifische Funktion oder einen individuellen Kundenbedarf
- Einzelanfertigung oder in geringer Stückzahl produziert.
- Hohe Anpassungsfähigkeit, aber auf bestimmte Prozesse beschränkt.
- Oft in spezialisierten Produktionsprozessen oder Nischenindustrien verwendet.
Beispiel
Eine Maschine, die nur für eine bestimmte Form des Prägens, Schweißens oder Stanzen eines einzigartigen Produkts eingesetzt wird.
Durch das kundenspezifische Standardsystem kann selbst eine hochspezialisierte Maschine von einer modularen Plattform profitieren. Hier wird es möglich, zentrale Module oder Baugruppen zu standardisieren, während spezifische Anpassungen nur für die besonders individuellen Anforderungen erfolgen. Das spart Entwicklungszeit und -kosten, ohne die Funktionalität einzuschränken. Zum Beispiel könnten Antriebs- oder Steuerungskomponenten standardisiert werden, während die Werkzeug- oder Bearbeitungseinheiten spezifisch auf die Aufgaben des Kunden zugeschnitten sind.
3. Serienmaschine
Definition
Eine Serienmaschine ist eine standardisierte Maschine, die in größeren Stückzahlen produziert wird und für breite Anwendungsbereiche ausgelegt ist. Sie wird in einer Serie hergestellt und ist so konzipiert, dass sie mit minimalen Anpassungen in verschiedenen Produktionsumgebungen eingesetzt werden kann. Serienmaschinen bieten in der Regel standardisierte Funktionen, die durch Optionen und Varianten erweitert werden können.
Charakteristika
- Standardisiertes Design, das in großen Mengen gefertigt wird.
- Flexibilität durch vorgegebene Optionen und Varianten, jedoch keine vollständige Individualisierung wie bei Spezialmaschinen.
- Kosteneffizient, da sie in Serie produziert wird und für viele Kundenanwendungen eingesetzt werden kann.
- Hohe Wiederholgenauigkeit und Zuverlässigkeit durch erprobte Konstruktionen.
Beispiel
Standardmaschinen für Verpackung, Abfüllung oder CNC-Bearbeitung, die für verschiedene Branchen und Anwendungen verwendet werden können, oft durch Auswahl standardisierter Optionen anpassbar.
Bei Serienmaschinen können durch ein kundenspezifisches Standardsystem die Module, die sonst als Varianten ausgelegt sind, flexibel ausgetauscht werden, um Kundenanforderungen gezielt anzupassen. Der Maschinenbauer kann Serienproduktion beibehalten, aber durch modulare Optionen höhere Flexibilität für individuelle Anpassungen bieten, ohne auf Serienfertigung zu verzichten.
Entdecken Sie die Vorteile des kundenspezifischen Standardsystems im Detail
Das kundenspezifische Standardsystem kombiniert die Vorteile von Effizienz und Flexibilität für verschiedene Maschinentypen.
Möchten Sie noch tiefer ins Detail gehen? Über den folgenden Link erhalten Sie umfassende Einblicke, wie anhand einer Spezialmaschine und einer klassischen Anlage die Möglichkeiten der Standardisierung, die daraus resultierenden Vorteile und das Vorgehen veranschaulicht werden.
Sie wollen mehr über die Tranformation Ihrer Produkte in ein "kundenspezifisches Standardsystem" erfahren?
Senden Sie mir eine E-Mail - ich melde mich bei Ihnen!
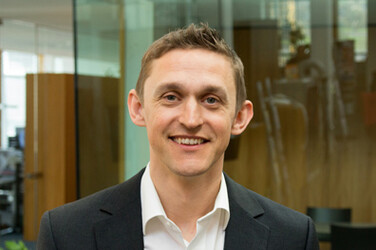